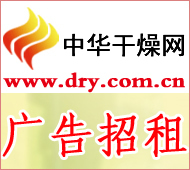
Hunan Zhuzhou Anbao Linfeng New Material Co., Ltd. mixed white carbon through wet mixing process and natural rubber latex to prepare a wet mix, which significantly improved the dispersion of white carbon in rubber, and made The mixing cycle is shortened by 1/3 and the compounding energy consumption of the compound is reduced by nearly 50%.
According to the company's general manager Mai Qianli, they took the lead in the domestic realization of the white carbon black and rubber compound wet mixing, that is, in the rubber is still in latex (natural latex or synthetic latex) added carbon black, white carbon, etc. The filler is mixed thoroughly and dispersed by stirring, and then a method of producing a mixed rubber by flocculation (coprecipitation) is performed. The experimental results show that the wet mixing process reduces the number of mixing stages and mixing time, can significantly reduce the mixing energy and cost of rubber, greatly improve the dispersion of various reinforcing fillers in rubber, and reduce dust pollution. It is conducive to the realization of continuous mixing process. In addition, the wet silica mixture has various degrees of increase in tensile strength, tear strength, elasticity, etc., and the rolling resistance of the rubber material has decreased by nearly 30% compared with the dry compound rubber. The load rolling temperature rise is reduced by 20%.
Mixing is the key process for the processing of rubber compounds, and it has always been the largest energy-consuming process in the processing of rubber compounds, and its energy consumption accounts for more than half of the entire rubber processing energy consumption. The common dry mixing method has a large difference between each batch of rubber compound, which often has a great impact on the quality of the subsequent process, and also produces a large amount of dust. It is the largest source of dust pollution for rubber and rubber products manufacturing companies. Silica reinforcing materials can improve the wet grip on tires and reduce rolling resistance. However, due to poor dispersibility when using traditional dry mixing, it has an adverse effect on many physical and mechanical properties of rubber compounds. Therefore, the rubber industry has been exploring and seeking to save more energy than the existing dry-process mixing process, so that the compounding agent can be better and more uniformly dispersed in the rubber.
It is understood that the wet blending method is not only suitable for natural rubber latex, but also suitable for styrene-butadiene latex or nitrile latex when properly adjusted. The process has recently obtained national invention patents.
E Bike Rear Light,Waterproof Safety Bike Rear Lights,Bus led tail lights,USB Smart Rechargeable Bike Rear Lights
NINGBO KLEANSOURCE ELECTRONIC TECHNOLOGY CO., LTD , https://www.ksledlight.com